Constructing Your Dream Home Faster with Prefab Methods
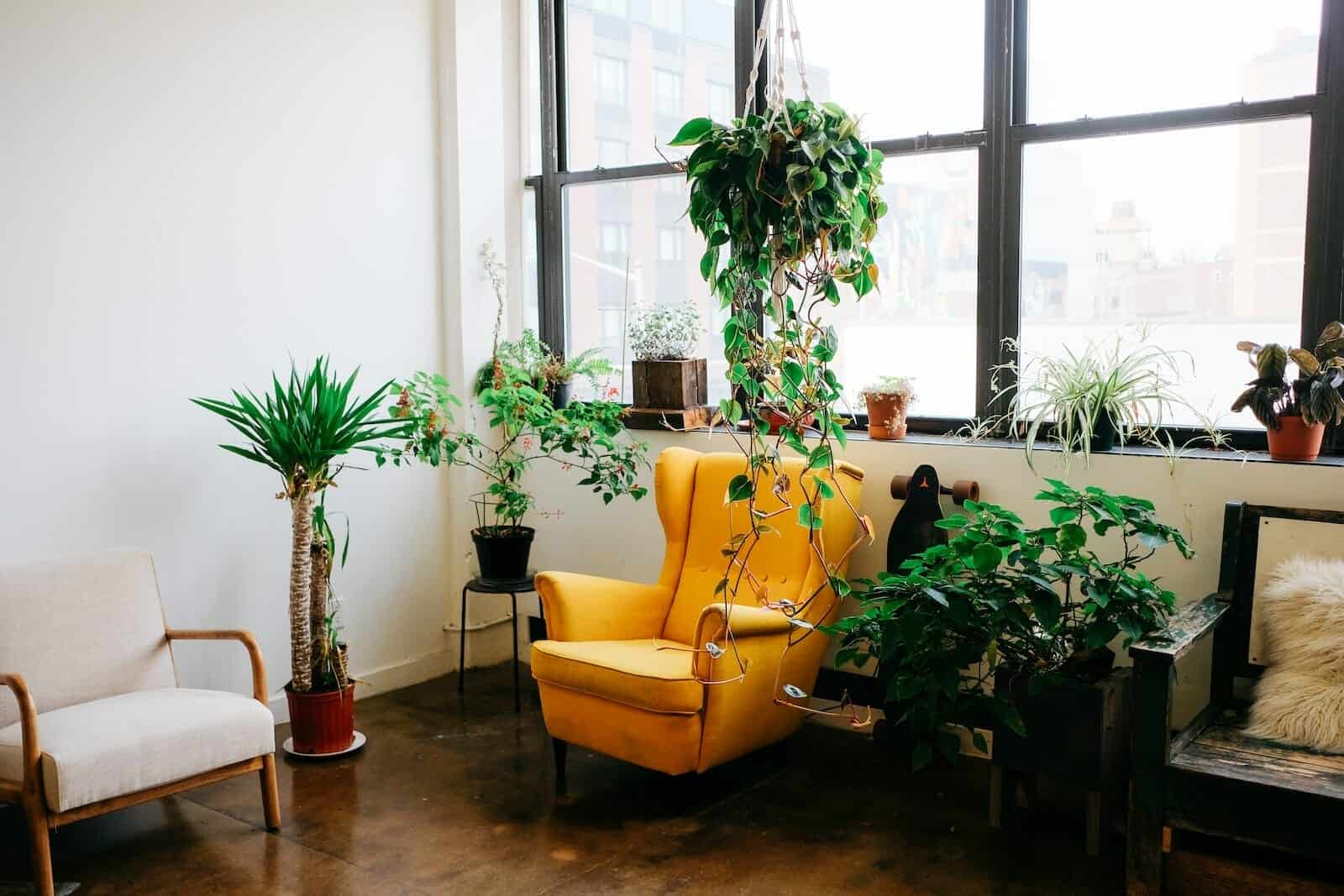
Floor Plan Options
Prefab floor plans include open concept single-story designs, multi-level plans, and options with multiple wings or sections. Plans can be tailored to suit:
- Number of bedrooms and bathrooms
- Spaces like a home office or gym
- Custom storage and closet solutions
- Flow preferences and indoor/outdoor connections
With a panelized system, nearly any floor plan is possible. Layouts accommodate disabilities.
Interior Finishes
Homeowners have extensive choice regarding:
- Flooring like hardwood, tile, or carpet
- Cabinetry styles from modern to farmhouse
- Plumbing and lighting fixtures
- Appliances and smart home systems
- Paint colors, wall finishes, and trims
- Bathroom and kitchen backsplashes
- And more based on your taste
Architectural Detailing
Unique architectural elements like rafter tails, decorative gables, dormers, columns, and trim accents can be incorporated. This allows designs like:
- Craftsman style bungalows
- Rustic mountain cabins
- Contemporary cubist designs
- Mediterranean or Tuscan villas
- And anything in between
Roof Styles
Choose from gabled, hipped, shed, or exotic roofs. Options like dormers, skylights, and complex multi-level roofs are possible.
Rooftop solar systems can be integrated into the waterproofing system. Roofing material choices range from asphalt to metal.
Facade Options
The exterior facade can be customized through:
- Mix of siding materials and patterns
- Fun colors and textures
- Corner boards, frieze, and trim accents
- Shutters, flower boxes, and ornamental railings
- Masonry elements like brick or manufactured stone
- And more to achieve your desired style
Today’s quality prefab builders allow extensive customization while still providing the benefits of offsite construction. The days of boxy cookie-cutter prefabs are over.
Conclusion
- Ability to adapt floor plans as needed
- Personal selection of all interior finishes
- Unique architectural detailing possible
- Custom roof shapes, elements, and materials
- Mix and match facade options for your style
Interested in having your dream home prefabricated? Here is an overview of the typical construction process:
Design Phase
This initial phase involves deciding on:
- Number of bedrooms, bathrooms, and other spaces needed
- Overall home size and square footage
- Architectural style preferences
- Customizations desired
- Budget parameters
With your wishlist in mind,floor plans are drafted and 3D renderings created. Your prefab builder provides design expertise and recommendations.
Engineering Phase
Once the preliminary design is approved, engineers generate technical drawings, determine structural loads, and specify materials needed.
They design structural wall panels, roof trusses, and other prefabricated components considering transportation limitations.
Engineers ensure the home meets or exceeds all relevant building codes and standards.
Production Phase
This is where the bulk of construction happens – at the prefab factory.
- Shop drawings guide each manufacturing station.
- Walls, floors, and roof sections are framed and insulated.
- Connections points and openings are prefabricated.
- Electrical, plumbing, HVAC, and fire protection systems are roughed-in.
- Exterior sheathing and moisture protection added.
Logistics Phase
The completed modular sections or panelized components are loaded onto trucks for delivery.
Specialty trailers safely transport units. Wide loads may need pilot vehicles and removable light poles enroute.
Local permits, road closures, and police escorts may be arranged. The logistics team oversees safe, on-time delivery.
Onsite Assembly
After foundation and utilities are prepped, the prefab components arrive.
Cranes lift sections into place. Crews interconnect units and tie into utilities.
Panelized buildings are erected and structural connections made. Weather-tight building enclosure achieved.
Finish Phase
Interior and exterior finish work happens concurrently.
Crews complete:
- Flooring, trim, doors
- Cabinetry, fixtures, appliances
- Painting, blinds, accessories
- Driveways, walks, landscaping
With coordination between your project team, site contractors, and prefab supplier, the manufacturing and building process results in your dream home efficiently delivered.
Conclusion
- Initial design and customization input
- Engineering for structural integrity and code compliance
- Factory prefabrication of modules or panels
- Logistics plan for safe delivery
- On-site assembly and structural completion
- Interior and exterior finish work
Prefabricated homes can be installed on several foundation types to suit the site, construction style, and budget. Here are some top options:
Poured Concrete
A traditional poured concrete perimeter foundation works well for modular prefab homes. Concrete offers:
- Long-term stability and minimal movement
- A smooth surface for precise module joining
- Excellent load-bearing capacity
- Permanence and rot/pest resistance
Footings are sized based on soil conditions. Walls are formed and poured, then backfilled. If basement space is desired, walls are waterproofed.
Prefab installers will bolt home modules directly to the concrete.
Reinforced Concrete Slabs
Concrete slab foundations are common in temperate climates. They offer similar strengths as perimeter foundations.
Reinforcing bars (“rebar”) cast into the slab prevents cracking. Thicker edge areas provide stability. Insulation under the slab helps moderate soil temperatures.
For modular construction, slabs may be further strengthened with embedded steel plates. These act as connection points to bolt modules to.
Pier and Beam
This foundation style uses spaced concrete piers, usually 1-2 feet thick, with steel rebar. Grade beams connect the tops of piers in a grid.
The prefab structure is then erected and floor framing attached to the beams. More piers may be added under major structural elements.
Piers work well on sites with expansive soils. They allow for some ground movement. Useful in flood-prone areas too.
Pile Foundations
Where poor soil or really uneven terrain exists, pilings may be used. This involves driving long steel or concrete poles into the ground to bearing soil or bedrock.
A deep pile cap then connects a group of pilings. Beams rise from the cap to support floor slabs or directly connect to modules.
While costly, piles allow construction on otherwise unusable sites. They can also raise homes above flood levels.
Strip Footings
Simple strip footings can work for panelized prefab systems with wood frame walls bearing directly on the foundation.
Trenches are excavated, forms erected, and concrete poured to create continuous footings under each wall.
Depth is based on frost line and soil strength. Light frame walls are anchored to the footing with bolts.
With prefab construction, foundation requirements are well-defined in advance. This allows selection of the optimal foundation type for your site and home.
Key Selection Factors
Choosing the ideal foundation involves assessing:
- Soil conditions and slope
- Local frost depth and climate
- Flood and seismic risk
- Construction style and loads
- Basement desires
- Initial and long-term costs
The prefab builder will guide appropriate foundation selection and design.
Conclusion
- Poured concrete for modular homes
- Reinforced slabs in temperate climates
- Pier and beam useful on expansive soils
- Pilings for problematic sites
- Strip footings for panelized buildings
Once prefabricated home sections are complete, the next vital step is carefully transporting them from the factory to the final site. This requires thorough planning and coordination.
Overview of Transportation Logistics
The logistics process involves these key elements:
Permitting – Securing necessary transportation permits for wide or overweight loads. Police escorts and temporary removal of road signs, lights, or utilities may be required.
Route Planning – Determining the optimal delivery route considering road widths, height clearances, bridge capacities, and work-around options.
Rigging – Lifting, loading, and bracing wall panels or whole modules using cranes and specialty equipment at the factory. Components are strapped down securely to flatbed trailers.
Transport – Trucking units via predetermined routes using proper pilot/escort vehicles. Additional route prep like filling potholes or trimming trees may be needed.
Unloading – On site, cranes lift units carefully off trailers and either temporarily store them or install them onto the prepared foundation system.
Modular Home Transportation
Modular units are typically fully enclosed homes with floors, walls, roof, and often interior finishes. They measure 14-16 feet wide and up to 80 feet long.
Multi-axle extendable trailers carefully transport each module. Tractor trucks capable of heavy loads are used.
Road travel usually happens at night to minimize impact on local traffic. Police manage needed road or lane closures.
Panelized Home Transportation
Panelized wall systems, roof trusses, and floor boxes are lighter and can use standard flatbed trailers. But lengths may still exceed regulated road limits.
Panels are commonly stacked flat on trailers. Some designs allow nested stacking to maximize loads. Tarps protect from weather and debris.
Final Mile Logistics
The final delivery from main roads to the building site is known as the “last mile.” This often involves small rural roads.
Temporary improvements like widening sharp corners may be required. Crews need to trim overhanging trees as well.
Sections are either craned directly into place or stored onsite until needed for installation. Logistics teams ensure efficient, safe end delivery.
Well-orchestrated transportation logistics are key to delivering prefab home sections damage-free while minimizing community impact.
Conclusion
- Advanced permitting, route planning, rigging
- Police escorts and utility/road modifications
- Multi-axle extendable trailers for modular
- Standard flatbeds for panelized but oversize
- Improvements to local roads for final delivery
- Just-in-time installation or temporary storage
While prefabricated homes offer faster, more affordable construction, there are some limitations and downsides to weigh as well:
Design Constraints
The modular construction process imposes some design restrictions. Dimensions are limited by road transportation regulations.
Plumbing and duct runs need to be contained within a module. Openconcept designs across units can pose challenges.
Complex rooflines and architectural elements may not be possible based on structural needs and assembly methods.
However, panelized systems allow more design flexibility with fewer long-span constraints.
Customization Limits
Modular prefab systems are not as customizable once main unit construction begins. Layout or finish changes can be costly and cause delays.
So modifications need to be finalized earlier in the process, with less opportunity to make adjustments once built.
Again, panelized designs allow more adaptability later in the schedule.
Upfront Planning Needs
A higher level of upfront planning is required with prefab. All design decisions must be made very early before factory construction commences.
Last-minute layout tweaks or material changes are not feasible. Time is needed to engineer each component.
With stick built homes, there is more flexibility to alter plans mid-stream. Prefab requires decisive vision early.
Site Constraints
Ideal sites are flat, open, and easily accessed by road. But many dream home locations are hillside, forested, or remote plots.
Extra site prep and grading may be needed for prefab modules to work. Overhead vegetation clearance, temporary roadways, and crane access are common requirements.
Panelized systems are better suited to constrained sites, but access is still a factor.
Single Source
With prefabrication, you are reliant on one company for design, manufacturing, logistics, and assembly. Quality depends on their expertise.
If after-sale issues occur, remedies may be limited. Traditional construction allows sourcing from many vendors.
Thoroughly vet any prefab provider on qualifications, experience, warranties, and client reviews before committing.
Prefab requires some design compromises and site constraints. But reputable prefab builders can overcome many limitations through quality engineering and construction.
Conclusion
- Earlier decision-making required
- Less flexibility once manufacturing begins
- Common design constraints to consider
- More complex site needs for access
- Reliant on single source for quality
Prefabricated homes differ from traditional construction, so extra steps should be taken to ensure your prefab home is top quality and built to last. Here are some tips:
Partner with a Reputable Builder
Vet prefab builders thoroughly. Seek companies with:
- A long, proven track record
- Extensive experience with complex projects
- An in-house engineering team
- Manufacturer certifications like ISO-9001
- Membership in trade organizations like MBI
Reviews from past clients provide insight on responsiveness and service quality after sale.
Evaluate Construction Methods
Look for structures built with sturdy framing and advanced sealing techniques like:
- Screwed AND glued fastening
- Seamless air barriers
- Redundant waterproofing
- Robust connections between modules/panels
This delivers durable, resilient buildings that stand the test of time.
Confirm High-Performance Materials
Specify durable, mold/rot/termite resistant materials:
- Kiln-dried framing lumber
- Galvanized steel connectors
- Closed-cell spray foam insulation
- Moisture-resistant exterior sheathing
- Composite exterior claddings
Avoid cheap products prone to early failure or leaks.
Demand Stringent Testing
The factory setting allows thorough testing of components before shipment:
- Structural load tests of frames and panels
- Air infiltration measurements
- Thermal imaging scans
- Water testing of enclosures
- Electronic systems function checks
This reduces onsite troubleshooting and ensures quality.
Verify Structural Engineering
Engage an independent engineer to review the proposed structural systems, load paths, and connections.
Verify design assumptions match your specific site parameters like wind, seismic zones, and soil type.
Solid engineering prevents issues down the road as the building ages and settles.
Plan for Onsite Inspections
Arrange follow-up site visits at key construction stages for your own quality assurance checks. Bring in a specialist inspector if desired.
Thoroughly check foundation, utility, envelope, and structural connections for any defects before covering up.
Keep quality assurance as a priority throughout the prefab design, manufacture, and assembly process to maximize your home’s longevity.
Conclusion
- Select only top prefab builders with proven records
- Scrutinize construction methods and materials used
- Demand extensive factory testing
- Verify independent structural engineering
- Perform thorough onsite inspections at milestone stages
Key Takeaways
Prefabricated construction offers dramatic advantages in speed and cost savings versus traditional building. However, prefab is still a comprehensive process involving:
- Multiple design iterations to maximize customization
- Structural engineering ensuring safety and code compliance
- Highly controlled factory assembly of modules or panels
- Complex logistics to transport units to site
- Coordination of foundation, utility, and assembly work
- Finish carpentry and detailing work onsite
Despite drawbacks like design constraints or upfront planning needs, prefab homes provide faster occupancy along with the quality and customization today’s homeowners demand. With careful process management and partnering with experienced prefab specialists, virtually any dream home can be realized through offsite construction.
Prefab has moved far beyond basic cookie-cutter designs to offer the innovative construction approaches and luxury finishes that discerning homeowners expect. Construction timelines under a year are possible while still delivering stunning, highly customized homes built to last using advanced methods. As technology progresses, the possibilities of prefabrication will continue expanding.
Conclusion
- Prefab combines speed and customization
- Engineering expertise ensures structural integrity
- Controlled factory production increases quality
- Logistics are key to safely delivering units
- Foundation and site prep precede assembly
- Finish work adds beauty and functionality
- With skilled partners, prefab limitations can be overcome
- Prefab innovations enable faster luxury homebuilding
Kontraktor Rumah Kabin
Rumah Kabin Murah
Rumah Kontena Vs Rumah Kabin
Rumah Kabin Pasang Siap
Senarai Harga Kabin di Malaysia
Heavy Duty Cabin
Light Duty Cabin